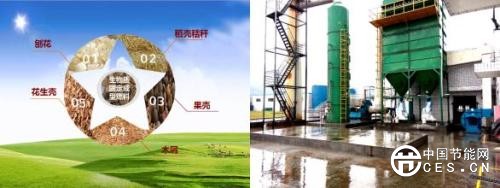
浙江、山东等省份的部分地区,与煤炭“超低排放”一视同仁的规则更让生物质企业深感不易。那么,其中的技术难点到底在哪呢?
韩某告诉记者,最难达标的环节在氮氧化物的处理上。中国循环经济协会可再生能源专业委员会副秘书长王卫权指出,目前,脱硝环节最主流的两种技术是选择性催化还原(SCR)和非选择性催化还原(SNCR)。小型装置可以直接氧化加压碱液吸收,理论上都能减少氮氧化物的排放,甚至达到“超低排放”的标准。
但在实际应用中,韩某表示:“生物质锅炉烟气中含碱金属、重金属等,采用选择性催化还原脱硝,易造成催化剂中毒甚至失效,还原剂同样会造成尾部受热面腐蚀以及堵塞,对温度窗口要求严格,炉温波动会造成脱硝效率低,无法达到超净排放要求。”
除技术因素外,王卫权也表示,在装备方面,“当前全国生物质燃料供热规模仍较小,而目前国内的脱硝设备大多是针对大型燃煤电厂,两者规模相差太大,其成本对生物质企业来说也就相对难以承受”。
达标排放难盈利?
面对“尴尬”的工艺和装备现状,基于环保的压力,全国生物质燃料企业却也不得不采取措施。
据悉,为达到“特别限值”的环保标准,韩某对其现有的3台蒸汽产能75吨/小时的生物质锅炉使用了“臭氧+等离子技术”进行脱硝处理。
“当烟气经过等离子烟气净化器时,在高压脉冲电场中,通过对烟气中含有的水、细微颗粒、氧气进行高压脉冲电晕放电,在常温下获得非平衡高低温等离子体,即产生大量高能电子以及极强氧化性能的羟基自由基等高能活性粒子。不仅对烟气进行了处理,净化了烟气,而且高能活性粒子大大增强其氧化性能。”韩某告诉记者,这一过程为臭氧对一氧化氮的氧化提供了良好的反应条件,提高了臭氧氧化氮氧化物的效率。“随后用射流喷嘴均匀注入臭氧,极短的时间内完成混合反应,将烟气中的NO转化成高价态的氮氧化物进入吸收塔。”
虽然已有技术路线和相应的尝试,但韩某指出,“生物质锅炉自动化程度相对较低,其尾气排放中污染物的含量也有所波动。自从今年6月新的排放处理设备投产以来,每月运营成本增加了约70万元,对本来利润空间就不大的生物质燃料企业来说,成本负担已达极限。”
同样,王卫权也告诉记者,目前,生物质燃料的原材料价格约为800-1000元/吨,生物质燃料通常由木质颗粒压制而成,而木质颗粒本身是一种具有经济价值的边角料,因此在原料采购方面就存在市场竞争关系,价格难以下降。尽管锅炉产能规模越大,收益越高,“但‘超低排放’标准对燃煤、燃气来说是合理的,对生物质锅炉来讲,直接要求‘超低排放’有点勉为其难。从理论上技术可行,但是经济上不可行。”王卫权坦言。“由于生物质燃料本身的燃烧特性,其锅炉产能目前最大就70吨/小时左右。对产能仅有1吨/小时的小规模生物质锅炉来说,“超低排放”标准则有些强人所难。”
此外,由于生物质燃烧后的烟尘颗粒物较燃煤排放更细,锅炉尾气处理装置中还需加上布袋除尘的设备,日常更换、维护设备同样会增加企业成本。
“生物质燃料锅炉‘超低排放’不是技术问题,而是经济问题。”在我国北方某生物质企业负责人的眼中,虽然其所在的省份尚未要求生物质执行“特别排放”、“超低排放”,但环保高压着实愈演愈烈。“排放标准不应该‘一刀切’,需要经过实际测算和科学评估,制定合理的生物质排放标准”。