玉柴飞轮集成发动机动力总成系统,可运用于多种构型的混合动力系统:混联式混合动力总成系统(P1+P2或者P1+P3方案)、增程器系统、并联式混合动力系统(P1方案)。可适应于客车、卡车、专用车、物流车等领域。
玉柴飞轮集成式电机在原发动机飞轮及齿圈组件上集成电机转子组件,在原发动机飞轮壳内部安装电机定子组件,可与发动机曲轴直连,在实现驱动和发电基础上具有以下特点:
① 代替原发动机起动机,具有起动发动机功能;
② 代替原发动机飞轮,保证发动机后端输出连接结构不变;
③ 整车在瞬态加速工况时,飞轮集成式电机可产生驱动力,助力发动机加速,实现机电耦合混合动力控制;
④ 整车在滑行和制动工况时,飞轮集成式电机可实现发电,在辅助整车制动的同时实现能量回收;
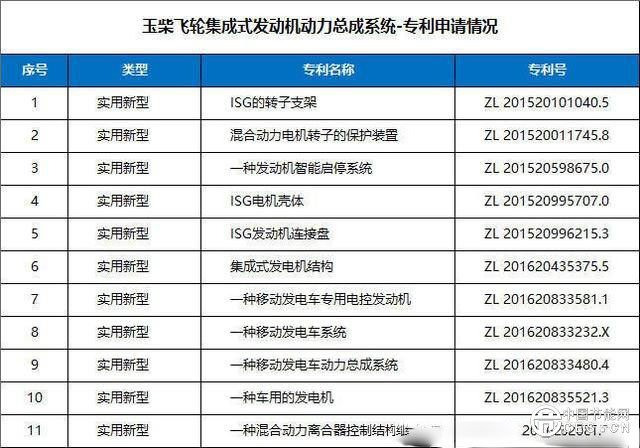
二、成果创新点及解决的难点问题
玉柴飞轮集成式发动机动力总成,创新点如下:
创新点一:结构紧凑,飞轮集成式电机采取飞轮集成电机转子组件,飞轮壳集成电机定子组件的措施,结构非常紧凑,长度仅为245mm,长度短、重量轻、能力损耗减少。
创新点二:发动机与电机的耦合式开发,飞轮集成式电机借助发动机支承,减少电机设计必需的电机主轴、轴承和端盖等,取消扭转减振器,飞轮集成式电机集成了起动机、飞轮及齿圈组件和飞轮壳;飞轮集成式电机转子可以满足发动机对飞轮的惯量要求,保证发动机对扭振、转速波动等方面的要求;(这种优势的取得,只有发动机厂家进行才最具备,单独电机厂家不具备。)
创新点三:瞬态性能(惯量)优势 ,飞轮集成式电机转子惯量与原发动机飞轮惯量接近,保持了原发动机的调速性能;传统电机方案的劣势为,发动机与电机相对独立,电机需要电机轴、轴承和端盖等零件,发动机需保留起动机、飞轮及齿圈组件和飞轮壳,两者在连接时需要增加扭转减振器,导致整个系统总成轴向长度偏长、重量偏大和零部件偏多等问题,存在整车动力系统总成布置困难、成本高、故障点多、维护复杂和响应性差等问题。
创新点四:可靠性优势,传统方案的劣势为,混合动力系统车辆行驶中发动机处于启动停止比较频繁的工作状况,过多的发动机反复启停使曲轴产生较大的扭矩载荷冲击,长此以往使曲轴发生断裂的风险提高;发动机在较低转速运行时,机油压力过低,长期工作会导致轴瓦早磨等故障。玉柴飞轮集成式电机可靠性优势 ,针对曲轴、轴瓦做相关设计改进工作,保证强度达到要求。
创新点五:成本优势 ,玉柴飞轮集成式发动机总成系统相比传统方案减少:飞轮齿圈组件、扭矩减震器等零部件,大幅降低成本。
三、国际水平对比分析
玉柴飞轮集成式发动机动力总成系统,在商用车领域,玉柴是国内唯一一家开发,也是唯一实现配套开发的厂家,申请并获得专利11项。在国际上,商用车领域,玉柴也是第一家把飞轮集成式电机产品商用化的企业。
四、成果应用情况
2017年玉柴飞轮集成式发动机动力总成系统已经实现小批,主要配套车型10~12米客车、18T卡车、牵引车、物流车等。
五、社会及经济效益分析
玉柴是车用动力的专业生产企业,有条件集中优势资源进行科技攻关和突破混合动力总成产业化生产的重大技术难关,促进和带动国内与之相关的产业链的发展。同时,不受制约于某种品牌整车的限制,能为国内所有的汽车厂进行配套与技术共享,拉动国内所有整车企业的技术进步与发展,对推动民族工业的发展将会做出重大的贡献。
玉柴有宽广的客户群体,容易形成批量大的生产,能有效地降低产品成本,提高产品在市场上的竟争力,从而获得良好的经济效益。
玉柴飞轮集成式发动机动力总成系统,可适用于多种混合动力系统,在混联式混合动力系统运用中具有较高的节能减排效果,以普通的12米城市客车为例,如年行驶里程10万公里,平均燃油耗约30L/100km,全年耗油3万升,按照平均60%的节油率来计算,每年可节省燃油1.8万升油,则当燃油价格为6元/L时,每年可节油10.8万元;同时还可以减少CO2排放28.4吨。
六、玉柴飞轮集成式发动机动力总成
应用场景1:混联式混合动力系统
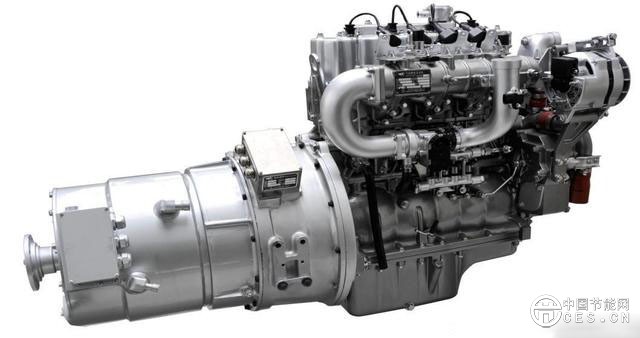
应用场景2:增程式系统
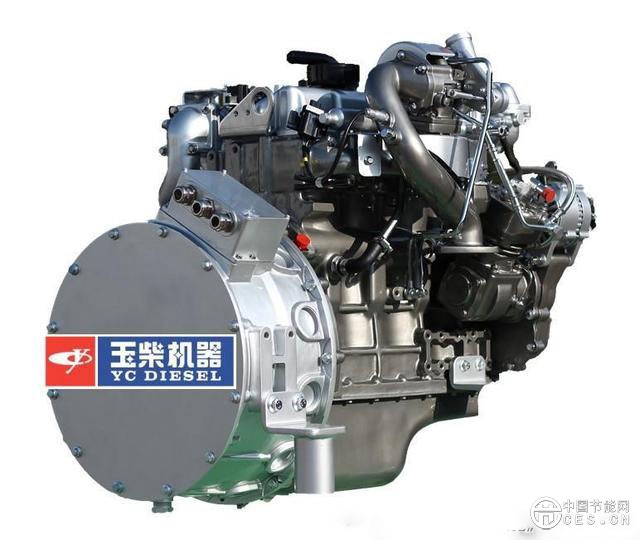