化工行业是水资源消耗大户,化工装置节水降耗是实现化工企业又好又快发展的重要保证,是提高化工企业竞争力和经济效益的客观要求,是可持续发展的出路所在。节水降耗的内涵就是优化结构,科学管理,技术进步,合理有效的利用水源;同时废水处理、中水回用的能力也反应了化工行业的技术水平、整体竞争力。
1、基本概况
1.1 原水
我们化工生产的原水主要是由净水厂处理后浊度≤5 mg/L的河水、矿井水和深井泵加压后的地下水提供。来自水厂的河水经水质水量调节、加药澄清、过滤、加氯杀菌后,汇集在原水池中,经加压站加压后,分别用作生产用水、生活用水、循环水补水和消防用水。地下水可以主要为降低夏季循环水温度,夏季全部送入凉水塔集水池,冬季部分送入循环水系统,另一部分送人原水吸水池中,与水厂送水汇合使用。原水池接受储存的原水也可以经水质、水量调节后进入脉冲澄清池加药澄清,再进入虹吸滤池过滤,加氯杀菌后进入储水池存储,经生活水泵、低压生产消防水泵、高压消防水泵、补水泵等功能泵加压输送后分别作为生活给水、生产用水、低压消防给水(新鲜水)、高压消防给水、循环水补充水供后续装置使用。
1.2 脱盐水
我们化工企业脱盐水系统普遍采用离子交换水处理工艺,每个系列流程依次有机械过滤器、弱酸阳床、活性炭过滤器、阳床、阴床和混床,采用PLC和S的控制操作系统。我们公司现有五个水处理系列,正常情况下两到三个系列运行,其它系列再生或备用,或者根据需要调整负荷。另外,脱盐水系统也可以采用先进的膜处理技术和离子交换除盐工艺。
比如使用荷兰诺瑞特公司生产的超滤膜元件,除去原水中大部分悬浮物、胶体及部分有机物。使用美国陶氏公司生产的反渗透膜,除去原水中95%的含盐量,再经阳床、阴床、混床进一步脱盐后作为锅炉给水。较常规离子交换除盐工艺大大减少了酸碱用量,减轻了环境污染。新鲜水(低压生产消防水)经多介质过滤器、活性炭过滤器过滤降低浊度、悬浮物后,进入RO反渗透装置进行预脱盐处理,75%的新鲜水制成了预脱盐水并去除掉97%的含盐量,之后预脱盐水进入离子交换装置进行二次脱盐处理,最终得到电导率(CD)<5斗S/cm,Si02<0.1 mg/L的脱盐水,脱盐水加压送至除氧器装置除氧后,再加压供锅炉、气化炉等装置使用;为了节能减排降耗,生产系统汽轮机冷凝液可以直接返回除氧器回收利用;中、低压蒸汽冷凝液回收至冷凝液槽减压闪蒸后用泵加压送到脱盐水装置,经精密过滤器、阴阳树脂混合床精制处理后进入脱盐水箱作为脱盐水进行回收利用,部分蒸汽冷凝液直接返至除氧器回收利用。
1.3循环水
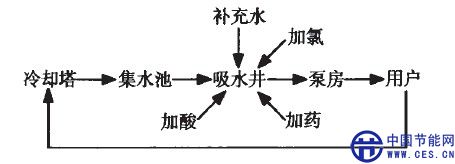
我们公司循环水系统采用机械通风敞开式循环冷却水处理工艺,采用多问逆流冷却塔。冷却塔集水池里的水经循环水泵加压后送往各用户装置,在与其他工艺介质换热后,汇人循环水回水总管中,经回水总管、冷却塔上水管线送到冷却塔与空气逆流接触冷却,降温后的水又汇集到冷却塔集水池中,经循环水泵升压后再送往各用户。为了保证循环冷却水水质防止腐蚀和结垢,系统设置加酸系统、加药系统、加氯杀菌系统,同时为了降低工艺循环水的浊度,分别设置排污及旁滤、补水系统。
循环水系统设计建设初期可以根据各生产装置对循环水参数要求不同的特点,将循环水管网分系统隔开,分为工艺循环水系统和热电空分系统。或者根据运行经验将热电车间与空分车间的循环水合并为净循环水系统,而将其他工艺循环水合并为浊循环水系统,充分考虑目前的污水回用问题,提升主工艺装置内水冷器的等级。循环水清、浊分流有效防止了各工艺装置因为工艺介质泄漏导致整个循环水系统污染的问题,同时也易于根据各生产装置对循环水压力的不同进行系统调整,便于污水回用工作的开展。
1.4 污水
我们公司污水处理系统采用A—O生物法处理工艺,SBR序批式间歇活性污泥法处理。在此分门别类探讨,以期抛砖引玉之功效。
1.4.1 工艺污水预处理
对于来自酚回收装置的工艺污水是高酚类、高COD、高NH,一N的污水,进人生化处理装置后首先在气浮池内加酸将pH值调节至水解池要求的范围,然后进入水解池及酸化罐。水解反应的主要作用是将废水中的大分子长链有机物分解为小分子短链有机物,改善废水的可生化性。酸化罐的主要作用是将不饱和有机分子转化为有机酸,酸化反应对部分有机物具有一定的去除功能,但主要仍是为了改善废水的可生化性。在水解酸化大大改善废水的可生化性后,工艺污水进入主体处理工序——多段
A/O的SBR生物反应器。污水在SBR池内通过好氧、缺氧交替作用,最大限度地去除污水中的有机物、NH,一N等污染物。该方法将进水、反应、沉淀、排水和闲置等工序集中同一反应池中,周期性运作完成对污染水的预处理。
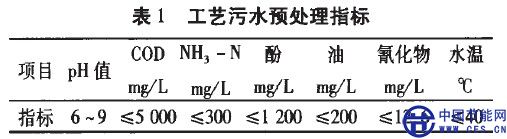
1.4.2 生产、生活污水预处理
来自厂区的生产、生活污水通过地下污水管网合并并重力自流进入污水生化装置,经格栅池除去大的漂浮物后用泵提升进入沉淀池,沉淀后的澄清水再用泵提升进入综合酸化罐,沉淀池沉淀收集的污泥送人污泥浓缩罐脱水处理。

1.4.3 合并处理
如果工艺污水完成SBR法预处理后,可以用泵提升进入综合酸化罐与生产、生活污水混合,在综合酸化罐中通过水解酸化改善生化性能后,靠重力流进入接触氧化池,接触氧化池主要处理有机污染物,同时对氨氮也有硝化作用。接触氧化池出水到二次沉淀池实现固液分离后,送至综合气浮池进一步去除剩余污染物质,再经氧化消毒、过滤后达到排放标准,一部分回用,剩余外排。我们这样做也为了节能降耗。
1.4.4 污泥处理
在生产中,我们生化处理装置还采用了污泥循环硝化技术。污泥循环硝化不仅可减少污泥最终剩余量,降低运行费用,减轻人工操作劳动强度,还可以提高前工序处理设施的处理效率,有助于提高废水的可生化性和处理效率。具体做法是:SBR池剩余污泥送入接触氧化系统,提高接触氧化系统的生物保有量;二次沉淀池污泥一部分返回水解系统,一部分返回接触氧化系统,剩余部分才与气浮、隔油沉淀污泥一起被污泥压滤机压缩为泥饼外运。
1.4.5 清污分流
我们对于污水来源为循环水排污、脱盐水制备废水、煤气系统的水封排放、不合格凝液排放、锅炉的连排定排、部分转机冷却水和工艺过程中产生的废水,其中高浓度废水主要有气体净化系统饱和热水塔含氨废水、合成蒸氨残液、尿素解吸废液、压缩机低压段含油废水、脱硫系统的脱硫残液、造气循环水系统溢流、电除尘冲洗水、水冷器的反洗废水、脱离子洗涤水等含有较高的氨氮或COD、石油类等;其它部分为水质污染程度较轻的污水,达到或者经简单处理后即可达到环保排放要求。废水执行环保排放标准为NH,一N≤15 mg/L,COD≤50 mg/L,pH值6~9,如果在早期建设中没有充分考虑清污分流,造成雨污不分、清污不分,终端污水处理进水量波动大,生产波动时,NH,一N、COD波动大,终端污水调整调节困难,排放指标时有超标。新建项目和扩能改造项目在设计时,排污管线可以考虑清污分流,但仍有部分高浓度废水需要排人终端,如果不将污染相对较轻的废水分离出来,将面临巨大的环保压力,同时污水处理成本的增加也会对消耗指标造成较大的影响。在此情况下,根据地形及主要排水单位布局、排污特点,在现有的设备设施和管道的基础上因地制宜进行改造,将从终端污水处理站进水中分离出部分废水直接排放,实现轻度污染废水从终端进水中的剥离,针对难以直接利用现有雨水系统进行排水的,清污水进行收集后增加设备和管道送人雨水系统。
通过清污分流可以减轻污水处理的压力,需要注意的是分出来直接进人雨水系统的轻度污染废水仍属于污染控制范围,所以轻度污染废水的水质指标(主要是环保排放指标)必须要保证稳定达标,避免出现指标波动影响总排口监测超标,轻度污染废水主要是COD控制,在清污分流改造的同时,对循环水的杀菌灭藻系统由原来的冲击式投加改为连续投加,COD由原来的80~90 mg/L降到了50 mg/L以下,当轻度污水水质指标恶化应有应急处理措施,避免环保指标超标。
2、技术改造的实践
2.1 水处理系统节能降耗技术改造
①循环水泵节能改造。循环水泵改成高效节能泵,正常投入使用,现场测量,能够达到设计指标,可以满足生产需要,就达到了节能降耗目的。②末端治理污水处理系统引进生活污水技改。脱盐水再生废水中含有氯离子较高,影响污水微生物生长,加上再生废水中碳氮比偏低等因素,出水指标达标率较低,引进生活污水改善脱盐水再生废水的可生化性,同时可降低废水的含盐量,宜于微生物的培养驯化。③循环水凉水塔水动风机改造。去掉电机动力驱动,利用上水压力带动水轮机做功,实现自然蒸发降温,达到节电的目的,风机运行平稳。④蒸汽冷凝液热能回收利用。脱盐水所回收的蒸汽冷凝液为低压蒸汽、锅炉联排、气化汽包水汽与甲醇装置工艺介质换热后的混合冷凝液,控制指标为:温度≤50 cC、电导≤10斗S/cm、二氧化硅≤100×10~。由于与甲醇工艺介质换热后冷凝液温度仍在90℃以上,为了降到回收温度,用循环冷却水换热,将温度降低至50℃以下。或者将原水引至蒸汽冷凝液冷却器,在冬季时用蒸汽冷凝液加热原水,一举三得:一是减少低压蒸汽的消耗;二是减少冬季循环水用量;三是节省换热器。⑤污水处理装置提标扩能改造。污水处理装置进行扩能改造,改造后污水处理能力不但能保证环保达标,还能做到节水降耗。
2.2 环保达标技术改造
我们集团部分化工生产污水处理系统曝气装置为射流曝气,充氧量不够、充氧不均匀;A/O池比例失调;B/C值0.15,难以生化处理。采取了以下措施,效果非常明显:①射流泵曝气装置改为微孑L曝气。②改现有A/O工艺为AI/01+A2/02+二沉池+重力无阀过滤器。③新增二级处理系统A2、02、二沉池。④新增重力无阀过滤系统。⑤增加事故缓冲池。⑥二沉池改为辐流式沉淀池,增加刮泥设备,⑦引进生活污水改善废水的可生化性,同时可降低废水的含盐量,宜于微生物的培养驯化。
循环水的水稳配方由磷系配方改为全有机膦碱性配方ZS401,如果循环水中氯离子、总碱度、总硬度含量明显增加,导致换热器严重结垢,热交换率低。从监测挂片的数据分析,铜的腐蚀率明显上升,为此,优选出适合水质的配方ZS402,在原配方ZS401配方的基础上增加了阻垢效果较好的磺酸盐成分,并增大铜缓蚀剂BTA的剂量,克服了原配方阻垢、缓蚀差的问题。随着环保排放要求的提高,又优选出适合水质的新配方ZS406,此配方属低磷环保型配方,总磷控制指标由原来的4.5~6.5 mg/L降到现在的1.5~2.5 mg/L,此配方使用后由于系统细菌的营养源减少,循环水的COD指标明显降低,异养菌指标合格率升高,循环水其它各项指标均能达到环保要求的控制指标的要求,从每次停车检修换热器打开的情况和每月的腐蚀挂片腐蚀率的数据看,效果较为理想,有效保证了各套装置的高负荷稳定生产。
3、化工生产水系统的实践经验
对循环水的指标进行分析检测,每当有漏氨发生时,采取了加大固体溴的投加量、氧化性杀菌剂和非氧化杀菌剂交替投加,并增大投加频率(采取杀菌一剥离一杀菌的加药方式),必要时对系统大排大补,有效地控制了菌藻繁殖。为防止系统腐蚀循环水增投缓蚀剂ZS2000,除采取以上措施外,还可以加强对浊度的控制,每周对滤池过滤器的进出口浊度进行分析,发现问题,及时进行强制反洗。循环水控制达到了防腐蚀、防结垢和杀菌的目的,确保各套装置的正常运行。
夏季为降低循环水温度,把温度较低的深井水全部切到循环水集水池,保证主装置高负荷生产。脱盐水系统节能降耗。①为保证脱盐水再生效果,又能做到节约,脱盐水系统采取现场测试再生废水的酸碱浓度,来控制再生时间的方法,降低了脱盐水消耗。②针对脱盐水阴床、混床出现二氧化硅沉积导致的出水硅超标现象,采用酸浸泡方法。
4、水系统的日常管理
4.1 重视管理和效果
重视水处理系统的日常工艺管理及运行效果,工艺技术人员组织班组对进出换热器的介质进行温度检测,并登记到帐,以能否满足生产需要为要求对换热器换热效果进行评价,对换热效果差的换热器积极协调清洗、清理,对不能隔离的换热器采取反冲洗或空气鼓泡等处理措施。给排水控制工艺指标要求建立统计台帐,利用电脑对每天统计的数据进行趋势分析,把握指标变化趋势,及时采取控制措施,在月底时对水质管理情况进行总结,弥补工作中的不足。中央化验室除按照分析频率对原水、脱盐水、循环水、污水等进行日常分析化验外,还开展全厂循环水换热器的查漏监测分析,各项分析结果均通过OA办公系统发送到中化生产日报专栏。
4.2 继续坚持对污水系统有组织达标排放
紧扣各个单元的污水排放设计指标,必须统一管理全厂污水的有组织排放,严格按照“谁装置区内的污水谁负责,不达标不排放”,杜绝超标污水进入污水处理系统,避免对污水处理系统造成冲击。
4.3 检修、工艺齐抓共管
通过设备包机制、消缺率考核、设备评级和零泄漏创建工作保证设备的良好运行状态,为水系统的稳定运行创造条件。充分调动工艺、检修人员积极性,强化设备日常维护,将设备故障解决在萌芽状态。
4.4 强化计量与统计管理
继续完善水系统的计量器具配置,准确进行水的利用分析、查找系统潜力和问题、监督和控制水量消耗。按照原水、生产水、循环水、脱盐水、工艺污水等介质分类,流量计可对不同工艺去向的水量分别计量,实现水量分级、分项考核的要求,每月根据各个工艺水量消耗情况依据内部市场化管理制度纳入成本消耗,以提高各个部门对水系统的重视程度。
4.5逐步实施污水的零排放,减少一次水用量,提高水的重复利用率
应国家可持续发展的要求以及企业的社会责任,必须考虑污水的零排放问题。但是由于污水零排放是一个系统工程,且实施耗资巨大,暂时考虑污水零排放分为以下几个步骤进行实施:
4.5.1实现污水的零排放
污水处理工艺是将工艺污水与生活污水最终混合处理后再回用至循环水系统。污水回用至循环水系统后,其排污水盐分将逐步提升至原来的3倍以上,同时由于系统浓缩循环排污水COD超出外排水指标要求,现其与生活污水混合后进人SBR处理后的工艺污水合并处理后再回用至循环水系统,如此反复必将加重回用水盐含量,最终导致因回用水盐分过高而无法满足回用要求。为解决此项问题,就需实施污水分质改造工作,将工艺污水与生活污水分质分别处理,将SBR/A池进行改造,由原处理工艺污水改造为处理生活污水,生活污水经此改造处理合格后直接排放至厂外,不再回用至循环水系统。从而实现工艺污水全部回用,而生活污水由于盐分偏高不再回用,而是合格外排。
4.5.2洁净废水回收再利用
脉冲池排泥废水、虹吸池反洗废水以及反渗透浓水,此部分废水污染程度轻,属洁净废水,经简易处理即可达到回用需求。反洗排泥废水可通过缓冲、沉淀等方式收集上清液返回原水大罐,反渗透浓水则通过超滤、反渗透工艺回收至预脱盐水箱,总体回收率在60%左右。改造后企业用水重复利用率提升13%以上。
4.5.3全厂排放水的回收再利用
排放废水占耗水量的1/4—1/3。污水来源按污染程度分为工艺污水、生活污水(含工艺界区冲洗污水、化验废水、初期雨水、浊循环排污水、生活污水)、清净废水(含原水预处理的排泥、反洗水、RO浓水、清循环水排污水、后期雨水)。以上三步实施后,工艺污水全部回用,全厂外排水成分主要为处理后的生活污水与浊循环排污混合水、原水预处理的排泥、反洗水、RO浓水、清循环水排污水、后期雨水,此部分水CD约4 000斗S/cm。此部分水可仿矿涌水的处理模式和管理运行模式,由专业水处理公司进行系统设计,回用率达到80%以上,改造后可每年减少原水需求,企业用水重复利用率提升36%以上,极大的节约了水资源。
5、水处理系统的系统管理
5.1做好污染源调查工作
我们在化工生产中,对于水系统制了“液相排放及装置用水点排查摸底”表,从排放去向、水质、水量等方面,对排水点分布、污水特点等进行细致的调查,对各事业部废水排放情况进行全范围摸底,汇编完整的资料,绘制公司污水管网图。摸底的同时,根据各事业部用水点水质要求,对部分废水进行综合利用,减少了废水排放量,降低总排排水压力。排查摸底过程中,坚持“不漏过一个地沟、窨井,不放过一个潜在用水点”的方针,通过“初审”、“复审”和“再查”三个阶段,完成废水数据收集工作,为公司确定废水处理及回用具体方案提供有力依据。
5.2进行技术改造,从源头减少排放,控制排放浓度
经过深入现场,了解第一手资料,确定环保重点难点问题。这些问题中,对于难点重点组织召开专题会议,制定出一系列技改方案并付诸实施。
5.3 强化制度建设与落实,努力创造特色管理模式
我们化工生产单位制定了《环保管理责任制》、《环保管理目标考核办法》、《环保管理目标考核细则》、《环保应急救援预案》等一系列管理制度及方案,对企业环保管理工作做出具体的要求,将总量控制指标和消减任务具体分解到各生产排污单位。各生产排污单位均绘制了从领导到操作人员的环保管理网络图,建立了基层环保管理责任制、环保应急救援预案、环保设施岗位责任制和操作规程。公司和基层各种环保管理制度作为一种基础管理经验,为公司发展多种产品产业、实现可持续发展提供不可或缺的理论基础保障。
5.4严格监督、检查、考核,遏制“三废”超标排放
我们公司结合环保专业管理制度,制定《环保管理考核办法》及考核细则,将各单位环保管理情况纳入环境安全建设工作,严格进行监督管理。为全面、准确地了解公司环保状况,将污水排放指标掌握在可控状态,公司实行环保状况周汇报、月督察、月考核等管理方式,由被动管理变主动管理,从生产污染源头抓起,杜绝污染事故的发生,基本遏制“三废”超标排放。
5.5地沟倒查、错时取样
为避免排放口加水稀释或隐蔽排放等现象存在,公司采取“地沟倒查”和“错时取样”的办法,多次查出取样时间之外排放口超标的问题,基本遏制了这一现象发生。
5.6工艺管理和设施设备管理并重,确保可靠、稳定运行
始终以生产运行为中心、设备管理为龙头,从污水调试启动直至日常运行的细小环节探索经验、总结规律,定期检查污水污泥处理过程、考核工艺运行效果,确保了工艺流程畅通、高效运行。在工艺运行管理方面,严格按工艺管理和调控规程进行调控和操作,明确了工艺参数和工艺调整的范围和程序,完善工艺控制手段和预防纠正措施。
5.7科学合理控制运行成本
生产过程中必须产生的运行成本主要由能源费用、材料费用、药剂费用、人工费用、检修维护费、大修及改造费、污泥处置费等构成。通过将电耗、水耗、维修材料、药剂消耗、备品备件等定期分析,针对性进行控制,同时消化吸收引进技术,在满足工艺运行和符合法律法规的前提下,不断提高设备国产化率。通过以上措施,确保高效、经济运行,使成本保持在较低水平。
6 、回用水处理方案的选择经验
6.1 回用水质要求
作为循环冷却水系统的补充水,它在系统中不断循环使用,由于水的温度升高、水流速度的变化、水的蒸发、各种无机离子和有机物质的浓缩、冷却塔和冷水池在室外受到阳光照射、灰尘杂物的飘人以及设备结构和材料等多种因素的综合作用,会产生比正常系统更为严重的沉积物附着、设备腐蚀和菌藻的大量繁殖,以及由此形成的黏泥污垢堵塞换热器等问题,它会威胁企业安全和长周期运行,甚至造成经济损失。所以必须对其进行水质稳定处理,保证生产装置的安全长周期运行。

6.2缓蚀方案的选择
从回用污水的水质可以看出,腐蚀离子主要来自硫化氢,硫化氢为弱酸性,硫离子强烈促进腐蚀,导致换热器局部腐蚀和氢鼓泡,并侵蚀混凝土。但硫化氢具有强还原性,可以被氧化沉淀出硫,而失去腐蚀性,同时,硫化氢还可以和很多二价金属离子生成硫化物沉淀,同样能使之失去腐蚀性。
根据硫化氢这一特性,我们在选择氧化性杀菌剂的投加方式时,有针对性的选择连续投加的方式,适当提高余氯的含量,充分氧化硫化氢,使之失去腐蚀性,同时适当提高了锌离子在药剂中的配比,进一步提高药剂的缓释效果。
另外,在含硫化氢的循环水中,单靠沉积膜型缓蚀剂很难达到理想的缓蚀效果,所以在配方中增加了氧化膜型缓蚀剂,将沉淀膜型的缓蚀剂、氧化膜型缓蚀剂和二价金属离子复合使用,同时抑制阳极和阴极的腐蚀,大大提高了药剂的缓蚀性能,确保了处理效果。
中水的油类也是导致腐蚀的一个重要因素,虽然油不直接参与腐蚀,但它容易粘附在设备表面,同时吸附水中的悬浮物,共同沉积在换热器表面,形成我们俗称的垢下腐蚀,同时石油类碳氢化合物是菌藻的营养源,如果得不到有效控制,它同样能加剧设备的腐蚀。在选择非氧化性杀菌剂时,特别考虑表面活性剂的功能,选择具有除油功能的表面活性剂,这样在杀菌灭藻的同时起到了除油的目的。
6.3阻垢方案的选择
从回用污水的水质看,虽然它属于中硬度水质,它的结垢趋势仍较严重,介质温度高,流速低的换热器更会出现结垢的可能。另外,回用污水的氨、铁离子含量较高,悬浮物、油等含量都会超出正常水质的指标,再有污水中的硫化氢会产生硫化物沉淀,这些因素都会导致污垢的大量沉积,所以,配方选择时,必须充分考虑阻垢,特别是分散剂的选择,尤为至关重要。
在阻垢和分散方面,选择PBTC、绿色环保的聚天冬氨酸和专有带示踪基团的磺酸盐共聚物,它们能够在高温、低流速等恶劣条件下,防止铁、钙、镁、锌和悬浮物等的析出沉积,从而保证了设备的换热效果。另外,从节水、环境保护和降低运行成本的角度出发,希望最大限度提高循环冷却水的浓缩倍数,浓缩倍数越高,结垢和污垢沉积的趋势越严重,当循环冷却水的pH值大于9.1时,适当加酸,提高处理效果,降低处理成本。
6.4杀菌灭藻方案的选择
循环冷却水中的菌藻和生物黏泥得不到有效的控制,将严重影响换热效果和腐蚀速度。针对化工循环水系统装置多、线路长、运行一定周期后容易出现微小泄漏、污水回用等特点,结合实际情况,采用氧化性杀菌灭藻剂(次氯酸钠)低浓度连续投加的方式,这样不仅可以始终将菌藻总数控制在一个较低数量有效抑制菌藻的繁殖,强化黏泥控制效果,而且可以氧化循环水中的硫化氢,同时可以将产生点蚀的可能性降到最低。另外视现场具体运行情况选用非氧化性杀菌剂交替冲击性投加,剥离粘附的粘泥的同时清洗系统中的油污,而且可以防止菌藻产生抗药性。
6.5药剂的投加及控制
三分药剂,七分管理,这充分说明了循环冷却水处理现场管理的重要性,而现场管理其中一项重要任务就是如何稳定控制药剂浓度,最大限度发挥水处理药剂的性能,保证处理效果,降低运行成本。
7、结论
总之,只要我们加强管理,不断技术创新,降低原水的消耗量、减少水的排污量,提高水系统管理水平,化工装置的安、稳、长、满、优、高效、低耗是完全可以实现的。只要我们勇于承担社会责任,就一定能够还我们的家园碧水蓝天!