二、适用范围:电力行业
三、与该节能技术相关生产环节的能耗现状:
目前成熟的脱硫技术如石灰石(石灰)-石膏湿法脱硫等虽取得了明显成效,但是投入成本高达亿元,成为目前制约火电厂配套脱硫设备的主要瓶颈。
四、技术内容:
1.技术原理
取消脱硫系统传统的GGH(气气换热系统),通过在吸收塔前加装烟气冷却器,其水侧与汽轮机的低压加热器系统连接,利用锅炉排烟余热加热部分或者全部凝结水,凝结水吸热升温后接入到下一级低压加热器,从而减少回热系统对低压缸的抽汽,在机组运行条件不变的情况下有更多的蒸汽进入低压缸做功,达到充分利用锅炉排烟余热的目的。同时,由于进入吸收塔的烟气温度降低,减少了吸收塔工业冷却水耗用量。
2. 关键技术
1)排烟余热利用:取消脱硫系统传统的GGH,通过在吸收塔前加装烟气冷却器,充分利用锅炉的排烟余热,提高汽轮机组的运行效率;同时,由于进入吸收塔的烟气温度降低,减少了吸收塔工业冷却水耗用量。
2)风机运行优化:在两台并联的增压风机基础上增加一条增压风机旁路烟道,并适当提高引风机的压头,通过优化风机的运行方式,实现在30%~60%BMCR 的低负荷工况下以单引风机运行代替双引风机+双增压风机运行,从而提高风机运行效率。
3. 工艺流程
1)排烟余热利用:在排烟余热利用方面,取消脱硫系统传统的GGH,改在吸收塔前加装烟气冷却器,其水侧并联在回热系统第二级低压加热器上,从2号低加进口引出部分或全部冷凝水,送往烟气冷却器。烟气从锅炉出来后,依次通过空气预热器、电除尘器和引风机,通过开启的脱硫入口档板进入到脱硫区域内,烟气经增压风机增压后进入到烟气冷却器内。从2号低加进口引出的部分或者全部凝结水在烟气冷却器内吸收排烟热量,降低排烟温度,而自身却被加热、升高温度后再返回低压加热器系统,在2号低加出口与剩下的凝结水汇集后进入到3号低加。气在烟气冷却器中降温后进入到脱硫吸收塔中进行脱硫,而后经脱硫出口档板至烟囱排放。同样,烟气也可不经过脱硫系统而直接通过脱硫旁路档板进入烟囱后排放。
2)风机综合优化运行:在风机优化运行方面,为了实现在较低负荷下的风机高效运行,必须增加一个增压风机的旁路烟道,在一定负荷条件下,烟气可以通过此旁路烟道绕过增压风机直接进入到烟气冷却器中冷却。在正常运行情况下从引风机A和引风机B出来的烟气分别进入增压风机A和增压风机B进行增压,此时增压风机A和B的入口档板打开,关闭增压风机旁路档板。烟气通过增压风机增压后再进入烟气冷却器冷却,冷却至85℃左右进入吸
收塔进行脱硫,而后经过除雾器和出口挡板至烟囱排放。在低负荷运行工况时,关闭两台引风机A,B的其中一台和两台增压风机,仅维持一台引风机运行,关闭增压风机A的入口挡板和出口挡板,打开增压风机B入口档板和旁路档板,让烟气从增压风机旁路烟道中通过。考虑到在增压风机B停运的情况下,增压风机B的入口档板长期处于开启状态会对风机叶片和机座等产生腐蚀,因此要求在单风机运行的情况下,始终保持增压风机B的出口档板处于
较小的开启状态,给增压风机B一定的烟气通流能力,防止腐蚀。这样,旁路烟道中的烟气和少量增压风机B通道中流通的烟气汇合后进入烟气热量回收器,冷却、脱硫后经烟囱排向大气。系统工艺流程图如下:
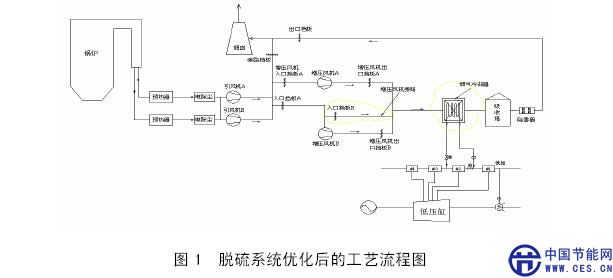
以2×1000MW 发电机组为例,采用本技术可使每台机组供电煤耗下降2.71g/kWh,年节电198 万kWh,年节水26 万t,取得综合经济效益2375 万元。
六、技术应用情况:
2009年5月在上海外高桥第三发电有限责任公司2×1000MW机组上首次应用成功。
七、典型用户及投资效益:
典型用户: 上海外高桥第三发电有限责任公司
建设规模:2×1000MW 机组。主要技改内容:烟气冷却器本体基础施工,烟气冷却器安装,凝结水管道和支吊架安装,烟道施工和风机改造(如有需要)。节能技改投资额4370 万元,建设期12 个月。按机组年利用5500h 测算,每年可节能29810tce,取得经济效益2276 万元,投资回收期2 年。
八、推广前景和节能潜力:
预计该技术到2015 年可推广10%,总投资约15 亿元,实现约90 万tce/a 的节能能力。