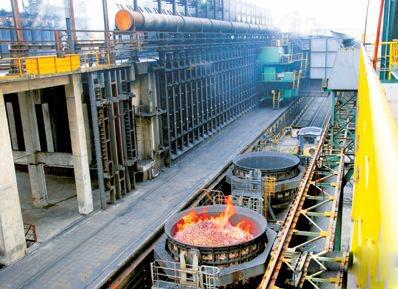
我国焦炭产量巨大,每年由此而产生的数百亿立方米焦炉煤气的综合利用已经成为我国炼焦行业必须关注的问题。根据焦炉煤气的特点(含氢量高),我国焦化行业 应进一步开发出符合企业特点的应用技术,进而实现煤气资源的优化开发利用,增加焦炉煤气的利用价值,增强炼焦行业的整体竞争力。近年来,我国焦炉煤气利用 程度不断提高,在开发利用技术方面进行了一系列的探索。
一、焦炉煤气用作气体燃料
焦炉煤气是优质的中热值气体燃料,其热值为17兆焦~19兆焦/标准立方米,煤气的主要成分(体积百分比)为氢55%~60%、甲烷23%~27%、一氧 化碳5%~8%,含两个以上个碳原子的不饱和烃2%~4%,以及少量的二氧化碳、氮、氧等。由于我国油气资源缺乏,为解决大中城市民用燃气紧张的问 题,20世纪80年代焦炉煤气曾一度广泛应用于民用燃气领域。目前,在天然气还没有通达而焦化行业有一定基础的地区,焦炉煤气仍是民用煤气和其他工业生产 的主要气体燃料提供者。如我国景德镇等地将焦炉煤气用作陶瓷厂窑炉的加热燃料,生产出优质的陶瓷制品。此外,焦炉煤气还可用作水泥和玻璃等工业生产的燃 料。
二、利用焦炉煤气发电
由于焦炉普遍采用了高效的烟气余热回收技术,约有50%~55%的焦炉煤气富余。我国许多焦化企业将剩余的焦炉煤气用于发电。焦炉煤气发电有三种方式,分别为蒸汽发电(热电联产)、燃气轮机发电和内燃机发电。目前这几种发电方式在国内均有应用,技术成熟。如果焦化企业与高电耗生产匹配或与发供电企业联营,且上网电价合适,焦炉煤气用于发电可作为优先选择的技术路线之一。其运行与管理简便,生产作业时间长,可采取多种方式,企业收益稳定。
1、蒸汽发电,热电联产供热与发电兼用。蒸汽发电由锅炉-凝汽式气轮机-发电机组成。该工艺以焦炉煤气作为热源燃烧锅炉,生成高压蒸汽,用以带动汽轮机、 发电机而发电。蒸汽发电技术过关、成熟可靠。在我国焦化行业应用较广泛,但其系统复杂、占地面积大、启动时间长。
2、焦炉煤气用于燃气轮机发电。燃气轮机发电是用焦炉煤气直接燃烧,驱动燃气轮机以带动发电机发电。燃气轮机发电机组设备紧凑、占地少、效率高、效益好、 启动速度快。不过,燃气轮机运行一段时间后必须远距离运回制造厂检修,因此需要较多的备品,要求工人有较高的技术素质。
3、燃气-蒸汽联合循环发电技术(CCPP)。该技术的基本原理是将剩余的焦炉煤气和回收的高炉煤气经净化、混合、加压后送往燃气轮机燃烧、膨胀做功,带 动燃气轮发电机组发电。同时燃气轮机排放的高温烟气加热余热锅炉,产生蒸汽,带动蒸汽轮发电机组,形成联合循环发电。燃气-蒸汽联合发电是热能资源的高效 梯级综合利用,其发电效率高达45%以上,实现了钢电联产,目前我国的济钢、宝钢、太钢、沙钢、通钢、鞍钢、马钢、邯钢、安钢、涟钢等多家钢厂都在使用该 技术。
4、用煤气内燃机带动发电机发电。我国山东、山西、宁夏、安徽、河北、新疆、内蒙古、云南、江苏等地的一些焦化厂采用煤气内燃机发电。可供选择的焦炉煤气 内燃机发电机组有400千瓦、500千瓦、1200千瓦和2000千瓦。目前焦化行业大多采用的是500千瓦焦炉煤气内燃机发电机组。按焦炉煤气热值(低 热值)16720千焦/立方米计算,1立方米焦炉煤气可发电1.1千瓦时。
三、利用焦炉煤气制氢
焦炉煤气中的氢含量达55%~60%,是重要的氢资源提供者。目前,焦炉煤气制氢(PSA)的主要方法是采用变压吸附技术从冷焦炉煤气中分离氢气,该工艺 生产的氢气纯度可达99.99%。从上世纪80年代开始,我国宝钢、鞍钢、武钢、本钢、包钢等钢铁企业先后建设了多套100立方米/时至5000立方米 /时、纯度为99.999%的焦炉煤气变压吸附制氢装置,其中投产运行时间最长的一套已达20多年。我国有多家钢铁企业采用PSA从焦炉煤气中分离氢气, 用作轧钢厂保护性气体。
据了解,日本钢铁行业每年提供约40亿标准立方米氢气供应给燃料电池行业使用,通过改进工艺,未来其供应量将进一步增加。另外,由于大多数日本钢厂位于城 市中心附近,所以未来城市所需的大部分清洁能源可由钢厂负责供应。在我国,随着氢电池开发、应用成本的降低,利用炼焦煤气提氢将成为焦炉煤气资源化利用的 新亮点。采用炼焦煤气生产氢气将是未来炼焦煤气资源化应用的新途径。
四、焦炉煤气用于生产直接还原铁
传统的炼铁工业完全依靠碳为还原剂,随着炼焦煤和焦炭资源的日益短缺,业界正在开发资源节约、环境友好的氢冶金,用焦炉煤气直接还原铁是氢冶金重要的应用 技术之一。由于氢的还原潜能是一氧化碳的14倍,大力开发焦炉煤气直接还原铁,可以大大降低炼铁过程对炼焦煤和焦炭的消耗。直接还原铁生产技术的关键在于 还原性气体(70%H2和30%CO)的制备,而焦炉煤气中H2和甲烷含量分别在55%~60%和23%~27%,只需将焦炉煤气中的甲烷进行热裂解(重 整)即可获得74%的H2和25%的CO,以此作为直接还原生产海绵铁的还原性气体非常廉价。
用焦炉煤气生产直接还原铁的研究以HYL-ZR(自重整)希尔工艺技术为基础,其通过在自身还原段中生成还原气体而实现最佳的还原效率,因此,该工艺无需 使用外部重整炉设备或者其他的还原气体生成系统。采用HYL-ZR(自重整)希尔工艺用焦炉煤气生产直接还原铁的生产成本较低,直接还原铁的金属率可达 94%。
五、焦炉煤气用于高炉喷吹炼铁
高炉喷吹含氢介质强化氢还原已成为当今冶炼工艺的热点。首先,无论从热力学还是从动力学条件看,高温下氢作为铁氧化物的还原剂比一氧化碳更具优势;其次, 氢还原的气态产物是水蒸气而不是二氧化碳,故喷吹含氢介质可减少二氧化碳的产生量。炼焦过程中,煤炭72%~78%生成焦炭,15%~18%生成焦炉煤 气。在炼铁过程中,焦炭的还原当量与焦炉煤气的还原当量之比为1∶1,因为H2的还原潜能与CO的还原潜能之比为14∶1。因此,将焦炉煤气通入高炉中同 样可以炼铁,相当于提高了炼焦煤资源的利用率,可缓解炼焦煤资源供应紧张的问题。
与天然气相比,焦炉煤气的还原性能更好。法国、俄罗斯等国已把高炉喷吹焦炉煤气作为节能减排关键技术进行开发,目前我国也已开始了高炉喷吹焦炉煤气的研究,钢铁联合企业的焦化厂应关注该技术的发展。
六、焦炉煤气作为化工原料生产合成气
近年来随着科技的进步与广大企业的勇于探索,焦炉煤气的应用领域拓展到制化肥、甲醇-二甲醚、提取甲烷制LNG和合成甲烷等。
1、焦炉煤气制合成氨—尿素。早在20世纪60年代,我国本溪钢铁公司第二焦化厂率先开发了焦炉煤气热裂解技术用于制纯氢,与空分氮气合成氨,进而生产尿 素。该技术较为成熟,很快推广至邯郸钢铁公司焦化厂、山西焦化集团有限公司和黑龙江化肥厂等。此后,由于国内化肥行业不断发展,以焦炉煤气为原料合成氨在 生产成本和销售市场等方面面临较大的竞争,所以很少有类似装置再建设。
2、焦炉煤气生产甲醇。每生产1吨甲醇可消耗焦炉煤气2000立方米~2200立方米,对富余的炼焦煤气消费非常可观。以焦炉煤气生产甲醇500万吨计 算,就可以消耗焦炉煤气100亿~120亿立方米。因此,利用焦炉煤气制甲醇、二甲醚、人造汽油等资源化开发利用比作为燃料具有更大的经济和社会效益。为 推进甲醇燃料的应用,国家先后出台了M15、M85等甲醇汽油标准,山西、陕西、河南等地已经开始甲醇汽油的车用试点。甲醇行业“十二五”发展目标将总产能控制在5000万吨,以焦炉煤气为原料生产甲醇所占的比例要由现在的10%增加到15%,而现在的煤基制甲醇要由38.2%下降到20%,天然气制甲醇要由28.2%下降到15%。
钢铁联合企业富余的焦炉煤气、转炉煤气生产甲醇。利用钢铁企业富余的焦炉煤气、转炉煤气或高炉煤气生产甲醇,是能源优化利用的新途径。该技术的关键点是采 用变温吸附法净化转炉煤气,使转炉煤气满足甲醇生产的要求。再将转炉煤气配加到焦炉煤气中生产甲醇,这一方法填补了我国利用转炉煤气和焦炉煤气生产甲醇工 业化的空白,为钢铁联合企业的富余煤气优化利用探索了一条成功之路。
3、焦炉煤气提取或合成天然气。在焦炉气组成中,甲烷含量约23%~27%,一氧化碳和二氧化碳含量占近10%,其余为氢和少量氮,因此焦炉气通过甲烷化 反应,可以使绝大部分一氧化碳和二氧化碳转化成甲烷,得到主要含氢、甲烷、氮的混合气体,经进一步分离提纯后可以得到甲烷体积在90%以上的合成天然气 (SNG),再经压缩得到压缩天然气(CNG)或经液化得到液化天然气(LNG)。焦炉煤气深度净化后经甲烷化生产天然气(SNG/CNG/LNG)的技 术,具有投资小、消耗低、无污染、能量利用率高等优势,是焦化企业较佳的选择。
目前焦炉煤气生产天然气主要有3种方式,分别为直接提取甲烷———天然气,提取甲烷富余氢气生产合成氨,焦炉煤气合成甲烷—天然气等。而焦炉煤气制天然气 的产品方案有3种,分别为合成天然气(SNG)、压缩天然气(CNG)和液化天然气(LNG)。生产1立方米天然气可消耗2.35立方米焦炉煤气,1吨 LNG(热值35.16兆焦/标准立方米)并副产1600立方米的副氢弛放气(热值10.32兆焦/标准立方米),须消耗3200立方米焦炉煤气。
七、焦炉煤气直接生产合成气
在焦化生产中,从炭化室经上升管逸出的650℃~700℃的荒煤气,在桥管和集气管中被大量喷洒的70℃~75℃循环氨水冷却至80℃~85℃,接着又在 初冷器中被冷却水冷却到25℃~40℃。650℃~700℃的高温荒煤气所带出的显热相当于炼焦过程总热量的32%,这部分能量几乎未被利用而白白浪费 了。
为充分利用这部分热量,20世纪90年代,德国提出建立生产两种产品———焦炭和还原性气体的焦化厂,即高温荒煤气从炭化室逸出后不冷却,直接进入热裂解 炉,将焦炉煤气中的煤焦油、粗苯、氨、萘等有机物热裂解成以CO和H2为主要成分的合成气体。这种合成气体可以作为生产合成氨、生产甲醇-二甲醚等的原料 气,也可以生产直接还原铁。
八、结语
日本煤炭能源中心在焦炉上进行单孔炉现场试验表明,煤气流量为400立方米/时~600立方米/时(即该炭化室煤气导出量的1/10),从焦炉炭化室出来 的高温荒煤气经转化炉实现了对焦炉煤气的重整,获得了体积百分比为氢68.0%、甲烷0.75%、一氧化碳22.7%、二氧化碳8.0%、氮气0.5%、 乙烯0.1%的合成气体。煤气中苯类可完全转化,煤焦油转化率95%以上。煤气利用可使煤气中的杂质大量减少,由于只有焦炭和合成气,也解决了一直困扰炼 焦行业的焦化废水处理问题。
一般说来,每利用1立方米焦炉煤气,可以节约0.6公斤左右标煤(焦炉煤气热值17兆焦~19兆焦/标准立方米),减少二氧化硫排放0.012公斤(以焦 炉煤气含硫化氢6克/标准立方米、噻吩、羰基硫、二硫化碳等有机硫230毫克/标准立方米估算)、减排二氧化碳0.79公斤左右(煤气组成受配合煤煤种与 质量、炼焦操作等因素影响,各企业的节能与减排效果,应按企业的实际情况测算)。
值得注意的是,近年来半焦(又称兰炭)炉装置的大型化和纳入《焦化行业准入条件》规范化管理以来,大型半焦企业生产富余低热值炼焦煤气的优化利用日益成为行业关注的热点。
“十二五” 期间,炼焦行业要坚持以科学发展为主题,以加快转变经济发展方式为主线,总结“十一五”行业发展的经验,积极推进技术与管理创新,努力构建资源节约环境友 好的新型焦化。坚持以《焦化行业准入条件》为抓手,开动脑筋,解放思想,广泛借鉴国内外一切科技成果为我所用,集中物力、财力与人力,整合炼焦研究资源, 开展适应我国煤炭资源与炼焦产业发展需要的综合性研究,探索新的炼焦煤气资源利用途径。