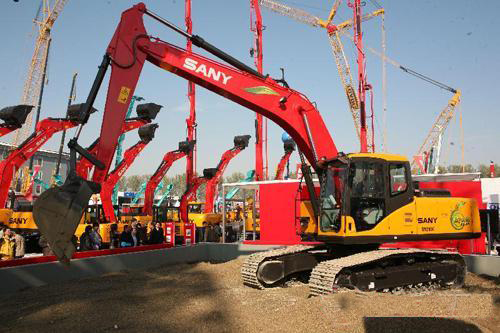
强制淘汰
根据国家推进节能减排工作的精神,有专家建议:参照汽车行业,通过法律手段,对老旧工程机械产品实施强制报废制度,有望从市场的角度助力节能减排政策的持续推进。
据介绍,目前老旧工程机械产品所配备的发动机大多从新机下线时就装配在产品上,这些内燃机的二氧化碳排放量远远高出现在的行业标准。老旧工程机械产品上使用的液压系统存在跑、冒、漏等现象,也是导致污染和资源浪费的主要因素之一。虽然这些配套零件可以通过更换得到解决,但如果将整机的液压系统全部拆除重做,成本将非常高。
专家认为,虽然我国工程机械市场的保有量在2000年以后才迅速攀升,但确定报废年限并非是为了淘汰已有老旧工程机械产品的权宜之计。再过几年,2000年以后生产的产品也将开始老化,当时使用的内燃机产品现在已不符合排放标准。而从2000年开始累计至今的产品数量已经很庞大,如果到那时再立法,付出的环境代价可能更大。对于主机和配套零件企业来说,如果实施报废制度,他们在更新生产设备时就可以放心大胆地淘汰落后产能,不必担心有用户需要对老旧产品进行维修时没有配套零件供给。这样就在减轻企业负担的同时,从生产源头加速了行业整体技术创新发展的步伐。另外,工程机械产品作业强度普遍较大,元器件和钢材的老化问题不可避免;部分产品的作业环境危险系数较高,这些因素给生产生活带来诸多安全隐患。

三大难题
工程机械产品实施强制报废制度固然有很多好处,但其实施的难度却也不小。因此,专家建议,实施工程机械产品强制报废制度需解决三大难题。第一要解决用户抵制问题。虽然强制淘汰老旧工程机械产品有诸多好处,但是工程机械产品是一种工业生产资料,它能给用户带来经济利益,多使用一次就可以获得更多的利益,用户是否接受强制报废制度很难确定。对于大、中型用户来讲,他们产品的更新周期相对较短,但只拥有几台产品的小企业或个体户就难免会存在抵触情绪。第二是二手市场难以控制。老旧工程机械产品不再通过主机制造企业流入市场,二手市场成为它们流通的主要渠道,因此,如何管理二手市场成为关键。控制这部分产品的流向非常困难,而这些产品恰恰对环境造成的污染最大。第三是产品分布太广,执法难度太大。有相当一部分工程机械产品流向矿山或其他偏远地区,执法力量能否覆盖这些地区很难确定。法律规定,带拖挂货车、矿山作业车的报废年限为8年,可申请延期至12年。事实上,这些产品多半使用不到报废年限车况就已经不行了,用户自然会及时将它们处理掉。但是诸如推土机、装载机等部分作业强度却相对较小的工程机械产品,可能使用十几年车况也不会有太大变化,如何监管这些产品也是一个难题。
标本兼治
正在进行混合动力尝试的企业越来越多,这是非常值得鼓励的。
但专家认为,这仍是一种治标不治本的方法。从环保的角度来讲,电力是清洁能源,不会产生尾气排放,也不会加剧温室效应。但是有一点不能忽略,那就是电池本身的环保问题。
专家表示,解决工程机械的排放问题必须从动力系统入手,但这个问题一直没得到内燃机企业的重视。工程机械产品的销量虽大,但与汽车行业相比仍是小巫见大巫,所以内燃机企业的研发重点一般都放在工作环境相对较为稳定的汽车行业。因此,解决工程机械节能减排的问题,需要两个行业乃至多个行业的通力合作才能成功。业内专家强调,在解决节能减排问题上,各企业应该积极拓宽思路,不能因为已经有了混合动力这一种方案就都闻风而起。毕竟,工程机械不是电动玩具,依靠电力运行只是权宜之计,每一种能够促进工程机械产品节能减排的方法都值得鼓励。
再制造铺路
据了解,我国工程机械设备大多处于超负荷工作状态。目前,全国已有80%的在役工程机械超过保质期,如果将被淘汰的装备产品进行修复,便能以较少的成本获取较大的回报,并减少能源消耗。有专家预测,中国工程机械再制造市场每年的规模可达100亿美元。
据介绍,工程机械再制造产品具有降低成本、节能环保两个鲜明的特点,是一种高端循环再生方式。用先进技术将废旧的机械设备按照制造业的模式进行彻底拆解翻修,生产出完全等同于新产品性能和质量的再制造产品,从而达到高效的二次利用。再制造产品利用尖端技术不仅能最大限度降低成本,还通过减少废物排放及降低对制造新零件所需原材料的需求,为环境保护提供了解决方案。作为再生资源利用的一种高级形式,再制造为发展循环经济、推动节能减排创造了条件。
资料显示,目前全球再制造产值已超过1000亿美元,有75%来自美国,其中汽车和工程机械再制造占2/3以上。在国外,再制造经过30多年的发展已经成为循环经济的重要组成部分。我国是装备制造及使用大国,设备资产已达几万亿元,14种主要工程机械的保有量达290万台。随着我国进入机械装备报废的高峰期,再制造产业显示出在社会、资源、环境效益等方面的独特优势。